Highly motivated undergraduate engineer with hands-on experience in manufacturing engineering. Proficient in Solidworks, AutoCAD, DFMA, GD&T, FEA, and Material Science
Manufacturing Engineer/Product Designer
(416) 721-8208
Email: michael@yetman.ca
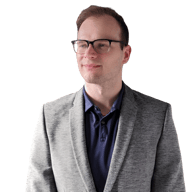
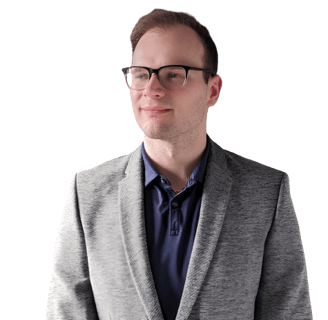
Michael Yetman
Certifications
✅ Certified SolidWorks Professional (CSWP) – Mechanical Design (Expected 2025)
✅ Certified SolidWorks Associate (CSWA) – Mechanical Design
✅ Lean Six Sigma White Belt
✅ Tech Stewardship Practice Program
Education
🎓Massachusetts Institute of Technology (MIT)
Architecture and Systems Engineering: Models and Methods to Manage Complex Systems (Expected 2025)
🎓 McMaster University – Bachelor of Technology in Manufacturing Engineering Technology (Expected 2025)
🎓 Humber College – Advanced Diploma in Mechanical Engineering Technology
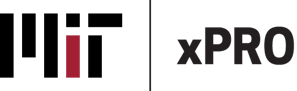
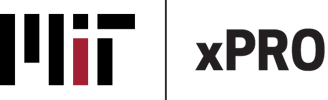
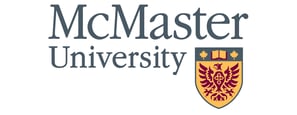
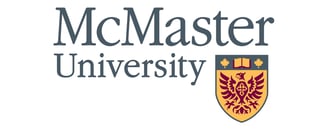
Solving Manufacturing & Product Development Challenges with Precision
In the world of manufacturing and product design, efficiency, quality, and innovation are key. I specialize in optimizing product development cycles, precision manufacturing, and design-for-manufacturing (DFM) to bring concepts to life in the most efficient and cost-effective way possible. Whether you're facing design inefficiencies, material selection issues, or production bottlenecks, my expertise can help you refine your processes and achieve high-quality, scalable solutions.
What I Do
Manufacturing Engineering & Process Optimization
I help companies improve manufacturing efficiency and reduce defects by implementing lean methodologies, Six Sigma techniques, and advanced manufacturing processes such as:
Design for Manufacturing & Assembly (DFMA) – Ensuring designs are optimized for cost-effective and efficient manufacturing.
Geometric Dimensioning & Tolerancing (GD&T) – Precision engineering that ensures manufacturability and assembly consistency.
Finite Element Analysis (FEA) & Computational Fluid Dynamics (CFD) – Predicting product performance under real-world conditions.
Root Cause Analysis & Failure Mode and Effects Analysis (FMEA) – Identifying and mitigating failure points in designs and manufacturing processes.
Material Selection & Optimization – Using Ashby charts and MatWeb databases to find the best material for performance and cost.
Product Design & Development
The product design process is part of a larger picture—the entire product lifecycle. It includes six stages: design, development, review, testing, deployment, and maintenance. Within the development stage, eight key steps transform an idea from concept to reality:
1. Conceptual Design
It all begins with rough ideas, sketches, and brainstorming. Here, we define the problem, user needs, and key product features. I utilize early CAD models and prototypes to shape the concept and validate feasibility.
2. Design Analysis
Once we have a rough idea, I conduct Finite Element Analysis (FEA) and Computational Fluid Dynamics (CFD) to simulate real-world conditions. This ensures the design can withstand mechanical stress, heat, fluid dynamics, and other operational forces.
3. Prototyping
At this stage, I use 3D printing, CNC machining, or manual fabrication to create prototypes. This hands-on approach uncovers hidden design flaws, usability challenges, and manufacturing constraints.
4. Production Drawings
Once the prototype is refined, I develop detailed manufacturing blueprints. These include dimensional tolerances, material specifications, and assembly instructions to ensure seamless production.
5. Material Selection
Choosing the right materials is critical. I use material databases (MatWeb, Ashby Charts) to evaluate options based on strength, weight, cost, durability, and environmental impact.
6. Pilot Production
Before full-scale manufacturing, I conduct a small batch production run. This allows for process validation, cost analysis, and quality control improvements before committing to mass production.
7. Production
Efficient manufacturing methods, including automation, additive manufacturing, and lean production techniques, ensure the final product is high-quality, scalable, and cost-effective.
8. Quality Assurance (QA)
A great design is only successful if it meets rigorous quality standards. I collaborate with QA teams to implement Six Sigma methodologies, automated inspections, and statistical process control (SPC) to guarantee consistent results.
How I Can Help You
Are you struggling with:
Reducing production costs while maintaining quality?
Optimizing a design for manufacturability?
Choosing the right materials for strength, weight, and durability?
Scaling up production while minimizing defects?
I work with manufacturers, product designers, and engineering teams to streamline their processes and solve technical challenges. Whether you need consulting, design expertise, or manufacturing process improvements, I can help you achieve your goals efficiently.
Industries I Work With
Aerospace – High-precision components, lightweight materials, and quality assurance.
Automotive – Cost-efficient, scalable designs for large-scale manufacturing.
Medical Devices – Regulatory compliance, high precision, and safety-focused design.
Electronics – Thermal management, compact design, and manufacturability.
Additive Manufacturing – Rapid prototyping, material innovations, and small-batch production.
Let’s Build Something Great
If you're looking for a solutions-driven engineer who understands both design and manufacturing, let’s connect. Whether it’s design consulting, process optimization, or full product development, I’m here to help.
Contact Me
📧 Email: michael@yetman.ca
🌐 Portfolio: https://michaelyetman.com/portfolio
🔗 LinkedIn: https://www.linkedin.com/in/michael-yetman/
Let’s turn challenges into opportunities and great ideas into real, manufacturable products.
Get in touch
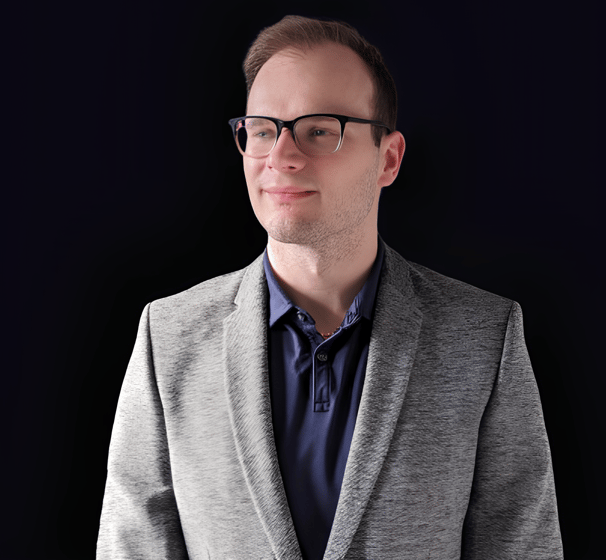
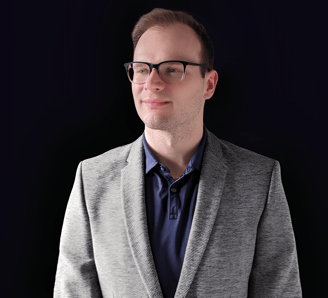